our mission: minimum construction for maximum development
the low cost, low carbon design & engineering solution revolutionising construction
- by using less than half as much material vs traditional concrete or steel structures
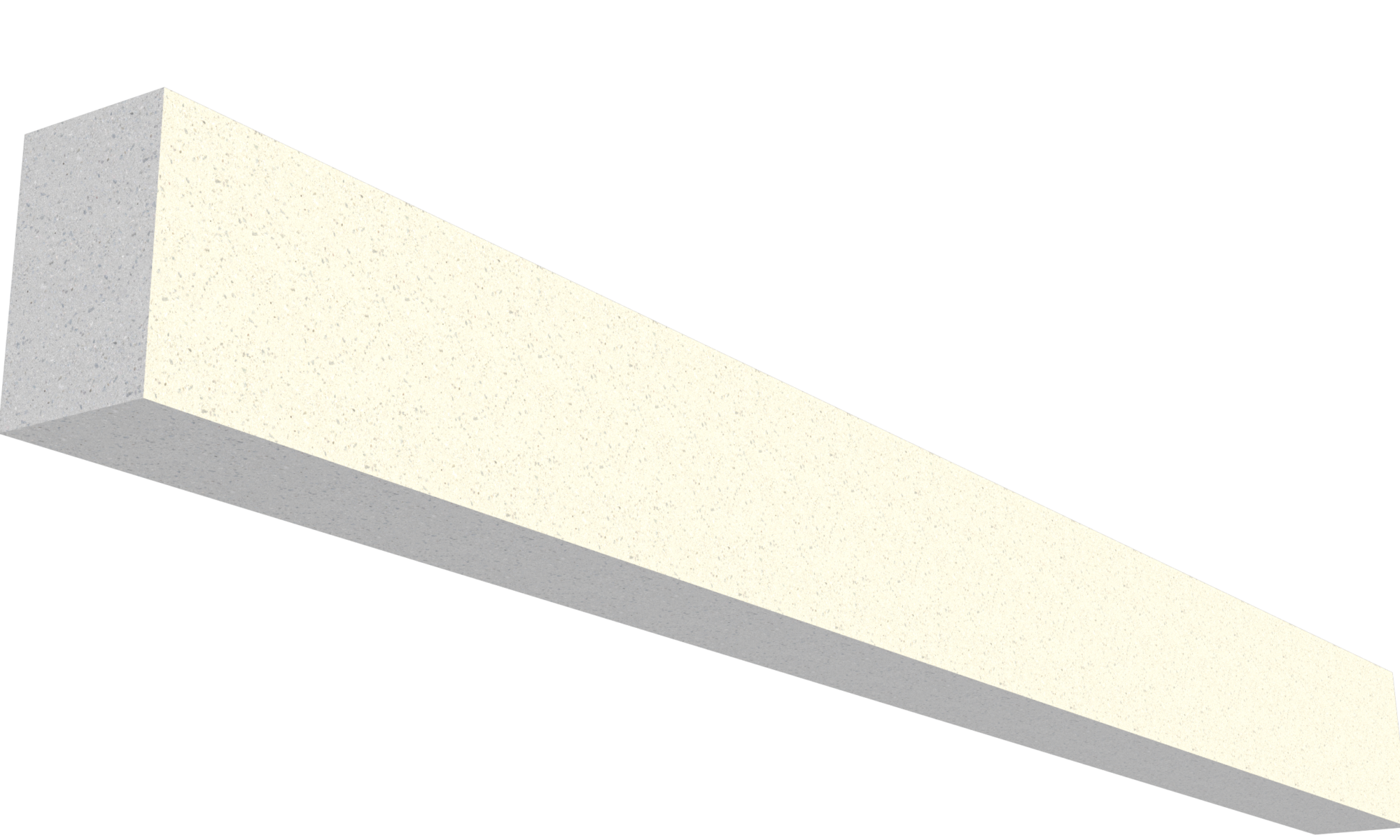
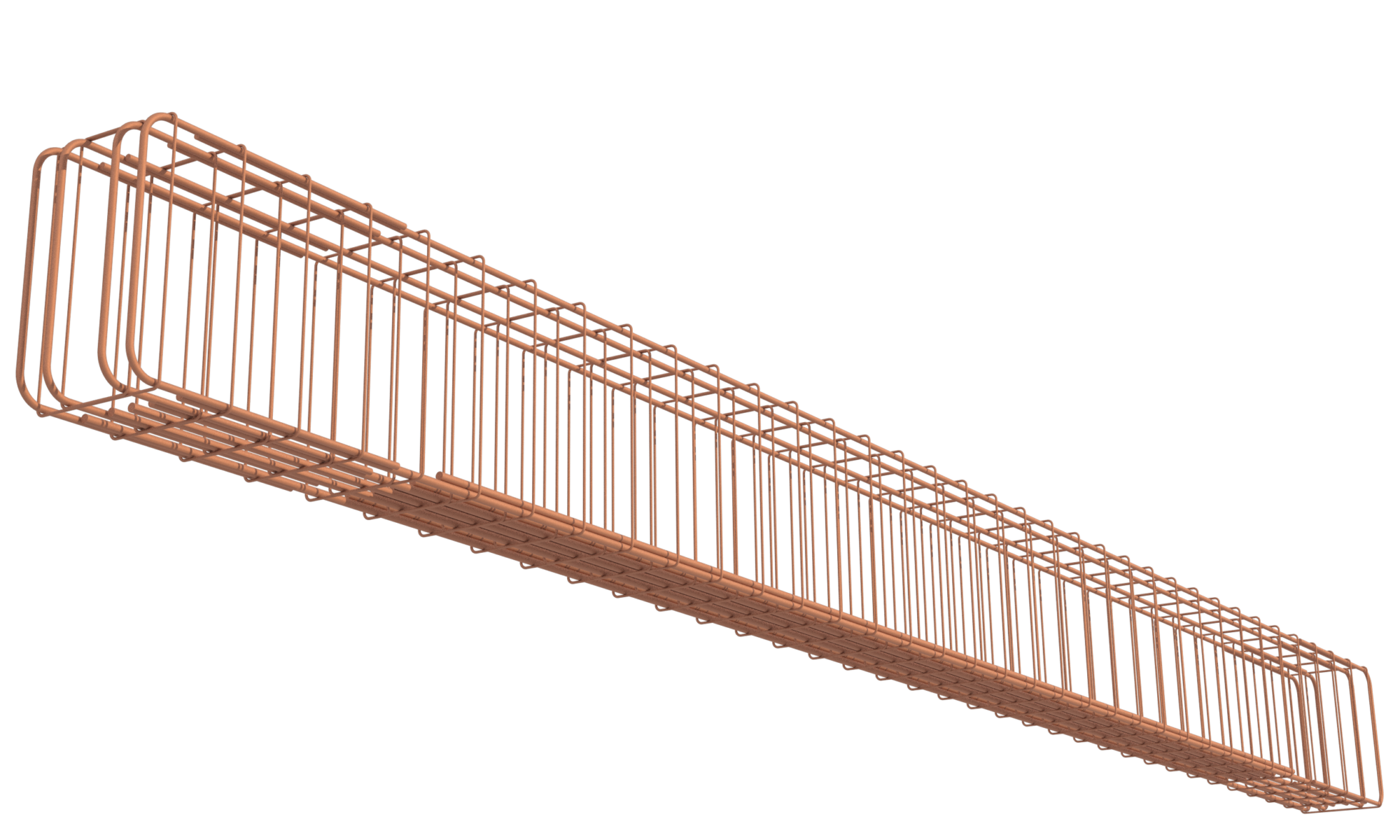
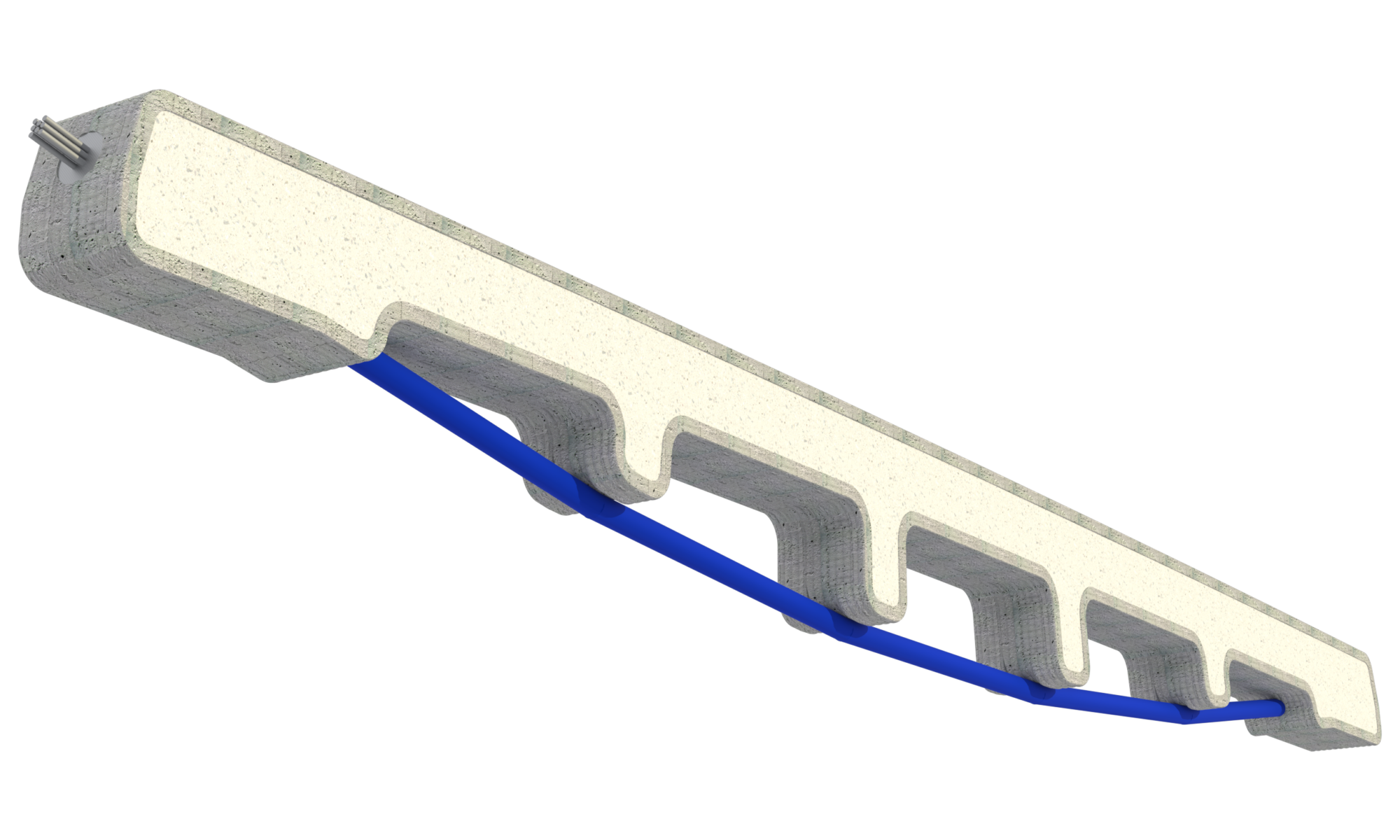
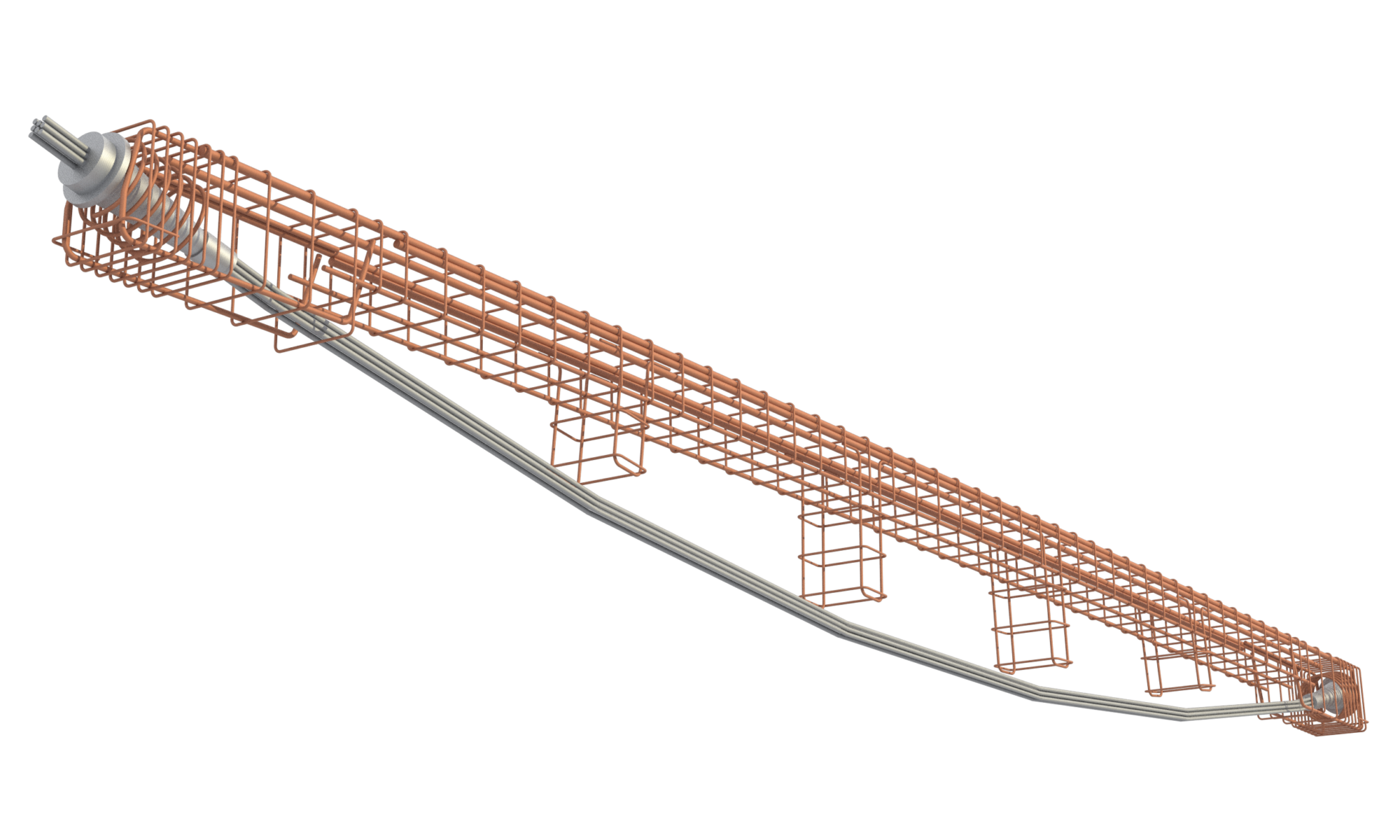
0%
reduction in concrete vs conventional concrete beam
trusted by contractors, developers & specifiers
including
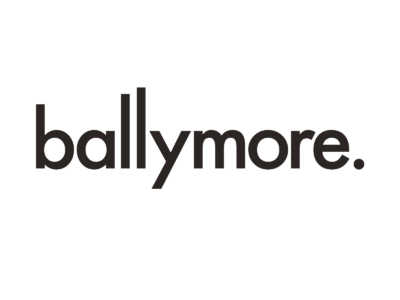
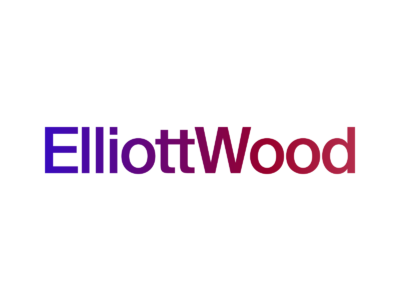
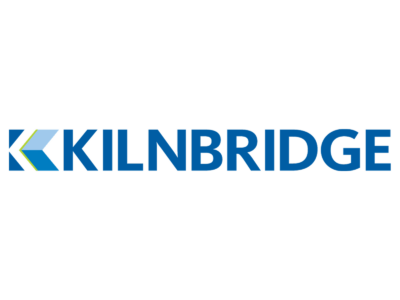
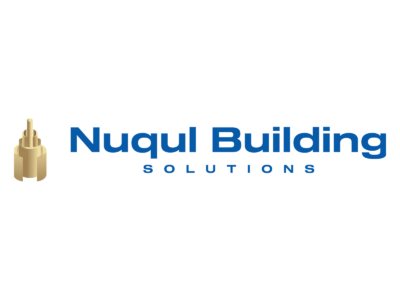
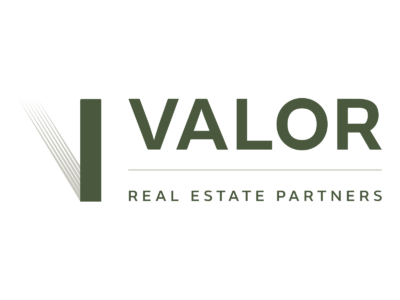
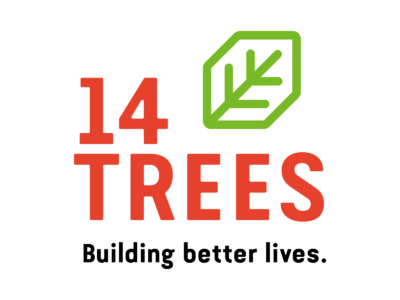
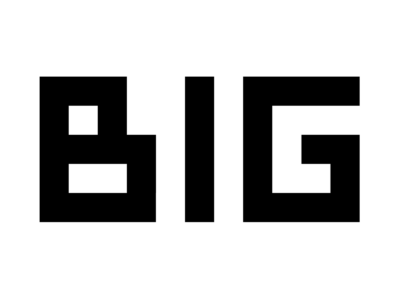
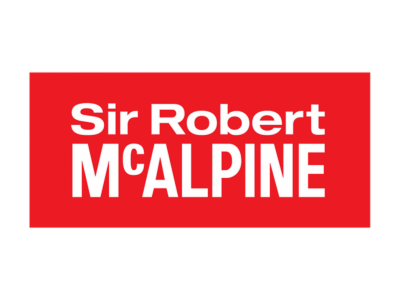
common construction industry problems
do these sound familiar?
low carbon options
usually cost more
winning tenders =
sacrificing profitability
no more low hanging
fruit to cut carbon
concrete's self-weight can
become prohibitive
key benefits for developers & contractors
vs traditional concrete / steel options for equivalent performance
up to 0%
lower cost
mainly due to the huge reduction in mass of material
up to 0%
lower carbon
embodied carbon levels are comparable with timber
up to 0%
fewer truck deliveries
and reduced cranage needs due to lighter weight
case studies by sector
applications include large buildings, bridges & temporary works - the longer the span, the better the savings
industrial & logistics
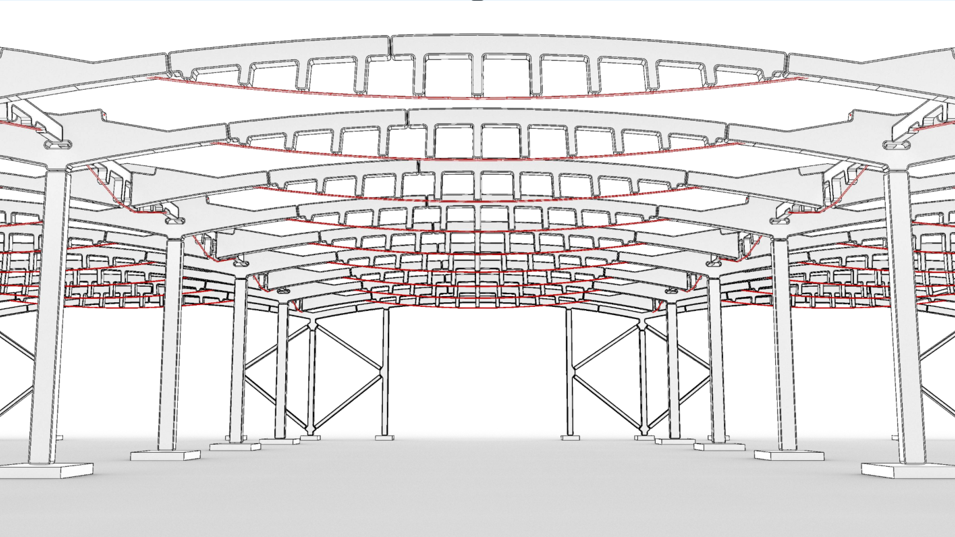
for the full frame, embodied carbon is cut by 44% and cost by up to 22% (including installation) for equivalent construction timeline vs a steel frame.
footbridges
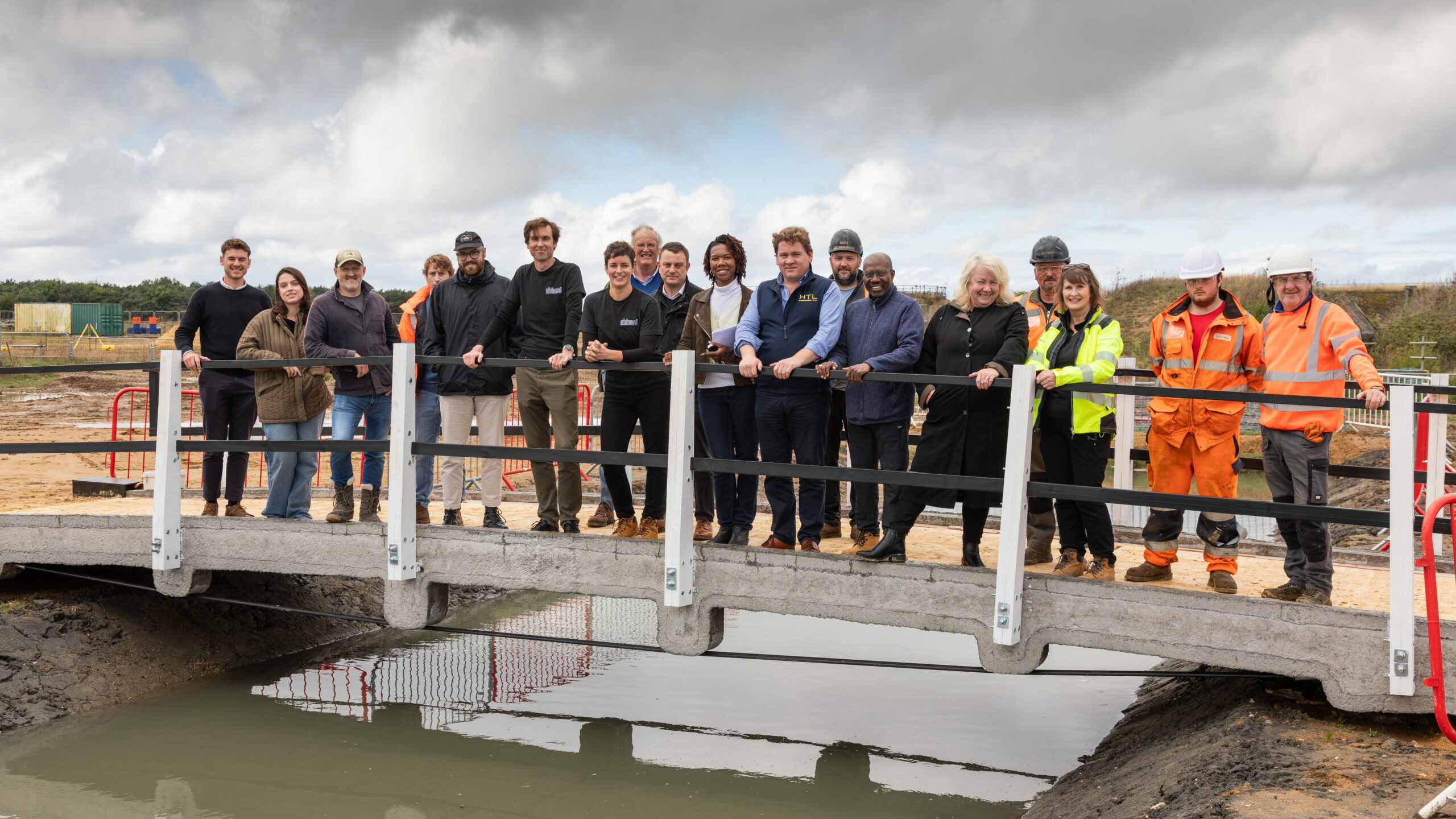
for the bridge as a whole, embodied carbon was cut by 30% and cost by 40% vs typical steel or concrete footbridges; for the beams, embodied carbon was cut by 50%.
road bridges
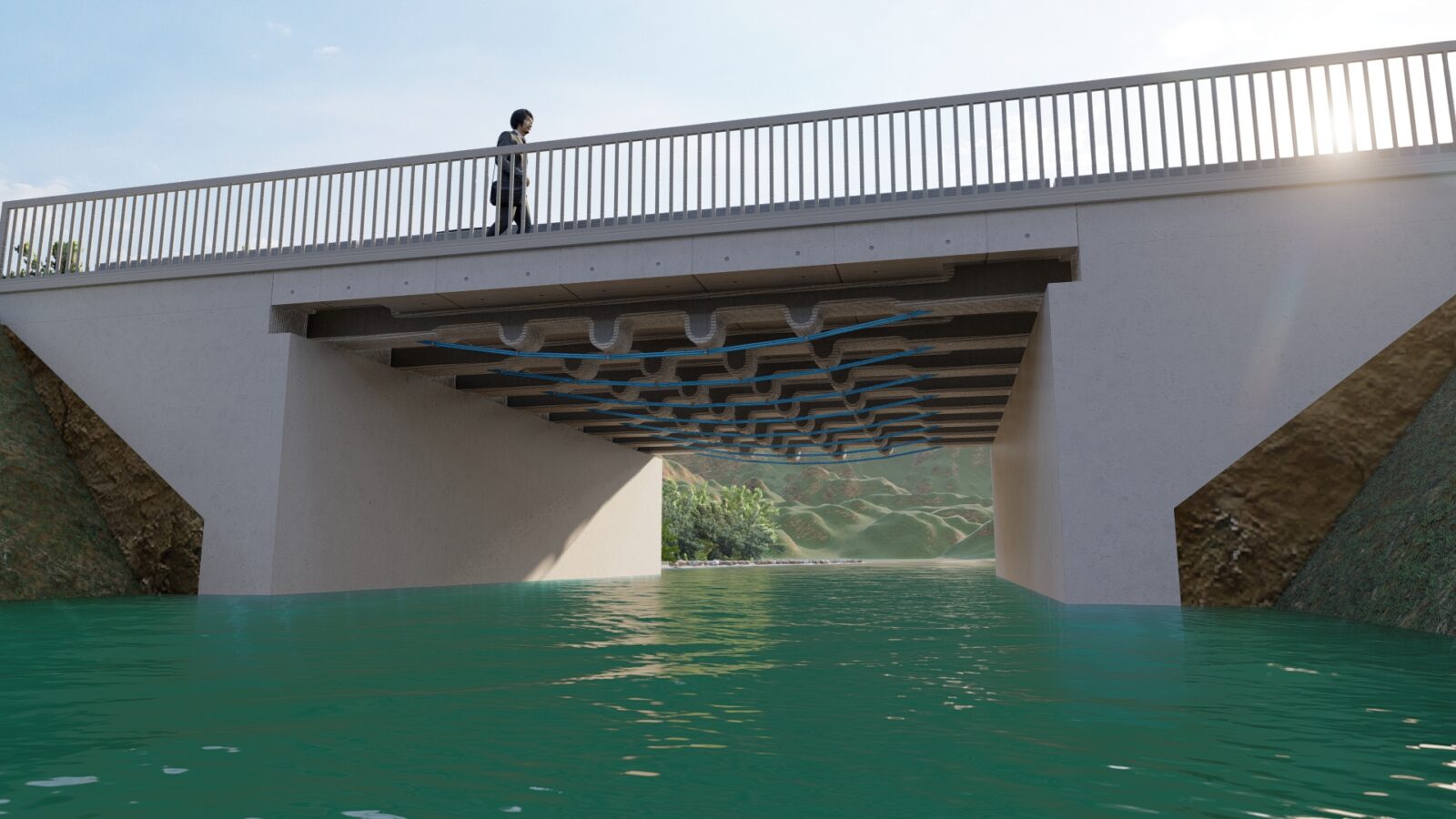
embodied carbon is cut by 38% and material costs by 31% vs traditional concrete beams.
minimass™ is a family of new prefabricated concrete structural elements (beams, frames & slabs) which replace any other type of structural elements.
patented in the UK, minimass™ combines 3D concrete printing with post-tensioning of steel to manufacture these structural elements in an innovative way. 3d concrete printing is an enabling technology, used to precisely place the concrete in compression, with no wasted material, and without complicated or expensive formwork for each bespoke element. PT steel tendons are then positioned in tension.
This allows a vast reduction in the amount of material used. For example, minimass™ beams deliver 50-78% less embodied carbon, and 20-40% lower supply cost compared to concrete or steel beams for equivalent performance and proportions.
minimass™ may be a new approach, but it is also familiar to the industry in terms of materials (concrete + steel), installation process (same skills as concrete) and geometry ("truss-esque").
minimass™ is the logical evolution of a design philosophy: use the right material, in the right place, for the right purpose – no more, no less.
11% of global carbon emissions come from construction, rising to 39% for the built environment as a whole including operational emissions [International Energy Association, 2019 Global Status Report for Buildings and Construction].
In order to reach Net Zero by 2050, the roadmap for the construction industry, from the Global Cement and Concrete Association (GCCA), requires a 25% reduction in emissions by 2030, compared to 2020.
minimass™ is the first product to realise the full potential of 3d printing for creating structural components. Sustainable development in the 21st century must include concrete solutions, but there is no need to wait until 2030 for meaningful reductions in embodied carbon. minimass™ provides savings of up to 70% – today.
minimass™ has been designed to replace any other type of beam. This means it is relevant for both large buildings (e.g. industrial & logistics, offices, retail, education) and bridge applications, as well as for temporary works. The geometry allows easy integration of services within the depth of the beam.
Examples of possible uses are:
· long-span portal frame for a warehouse e.g. case study for a 36m x 15m grid: minimass portal frame design
· beams to support precast concrete floors e.g. hollowcore
· beams to support CLT slabs, to increase the size of the column grid
· long-span floor beams e.g. in airports with 18m+ grids
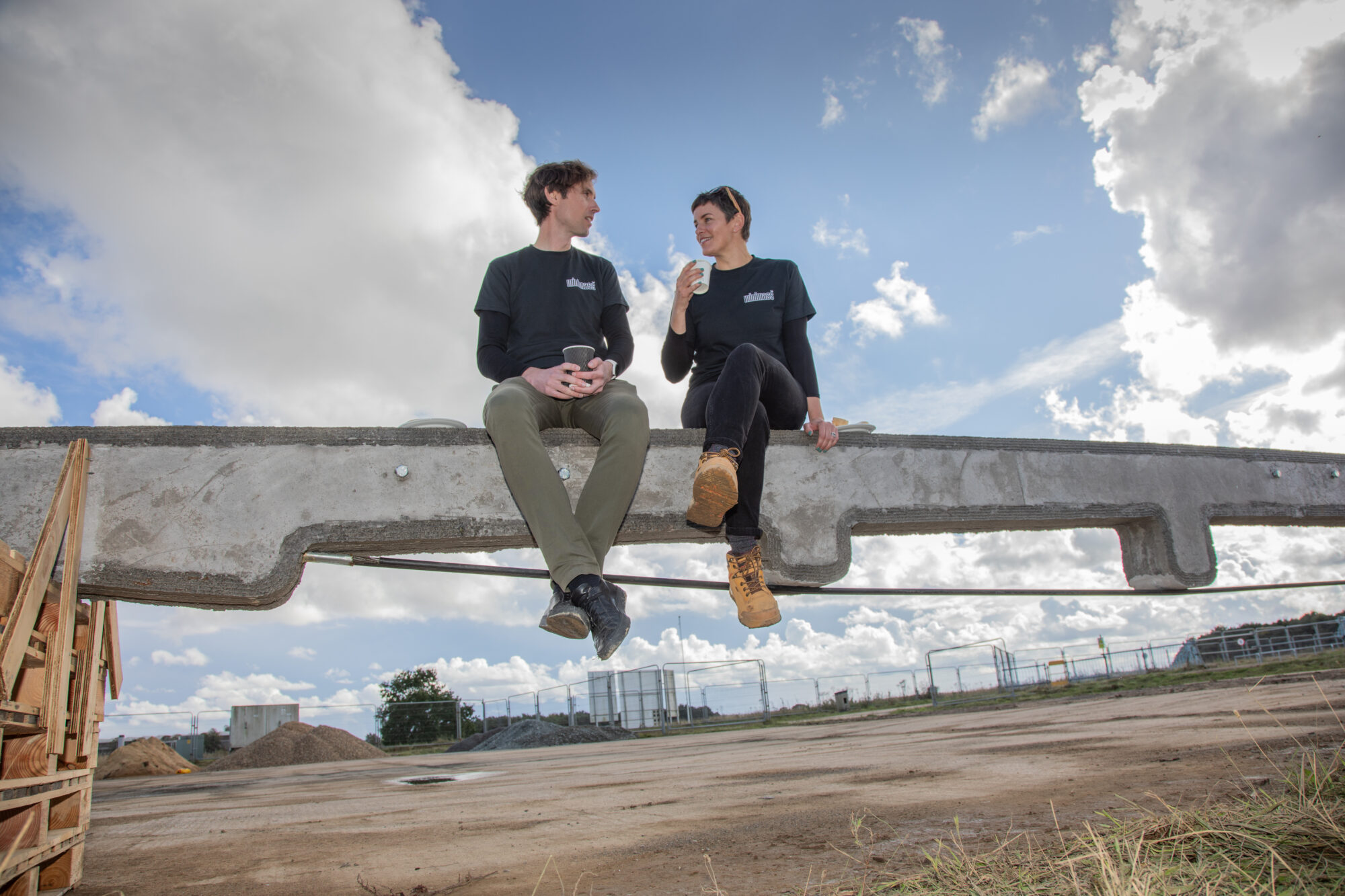
minimass™ was created by Andy Coward, Founder & CEO of the company Net Zero Projects Limited.
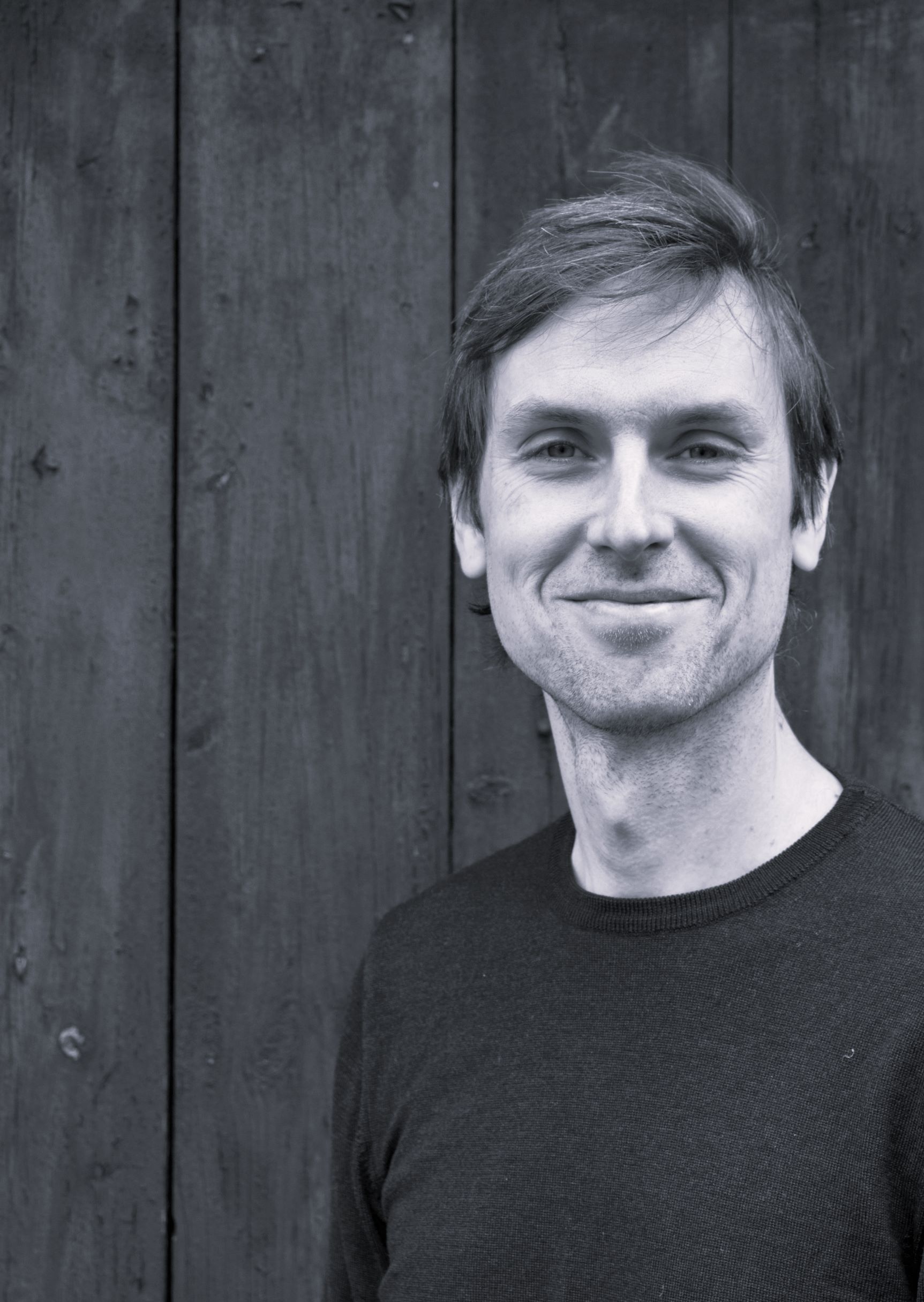
Andy holds a 1st class degree in Civil and Structural Engineering from University of Cambridge and has 20 years’ industry experience in design and construction. Prior to inventing minimass, he was Director of Engineering at Bjarke Ingels Group in Copenhagen, and Associate Partner at Foster + Partners in London.
Notable projects include:
· Tocumen International Airport, Panama
· the Orb at Burning Man festival, Nevada USA
· L’Ombriére, Marseille Vieux Port, France
· Health Pavilion, Cleveland USA
· Spartak Moscow football stadium, Russia
· Apple Stores, global.
Sarah Blake joined the business in September 2023 as Commercial Director & Co-founder. Sarah brings 11 years’ commercial real estate experience across several roles at British Land (including insights, business development & CRM), where she was part of the senior leadership team.
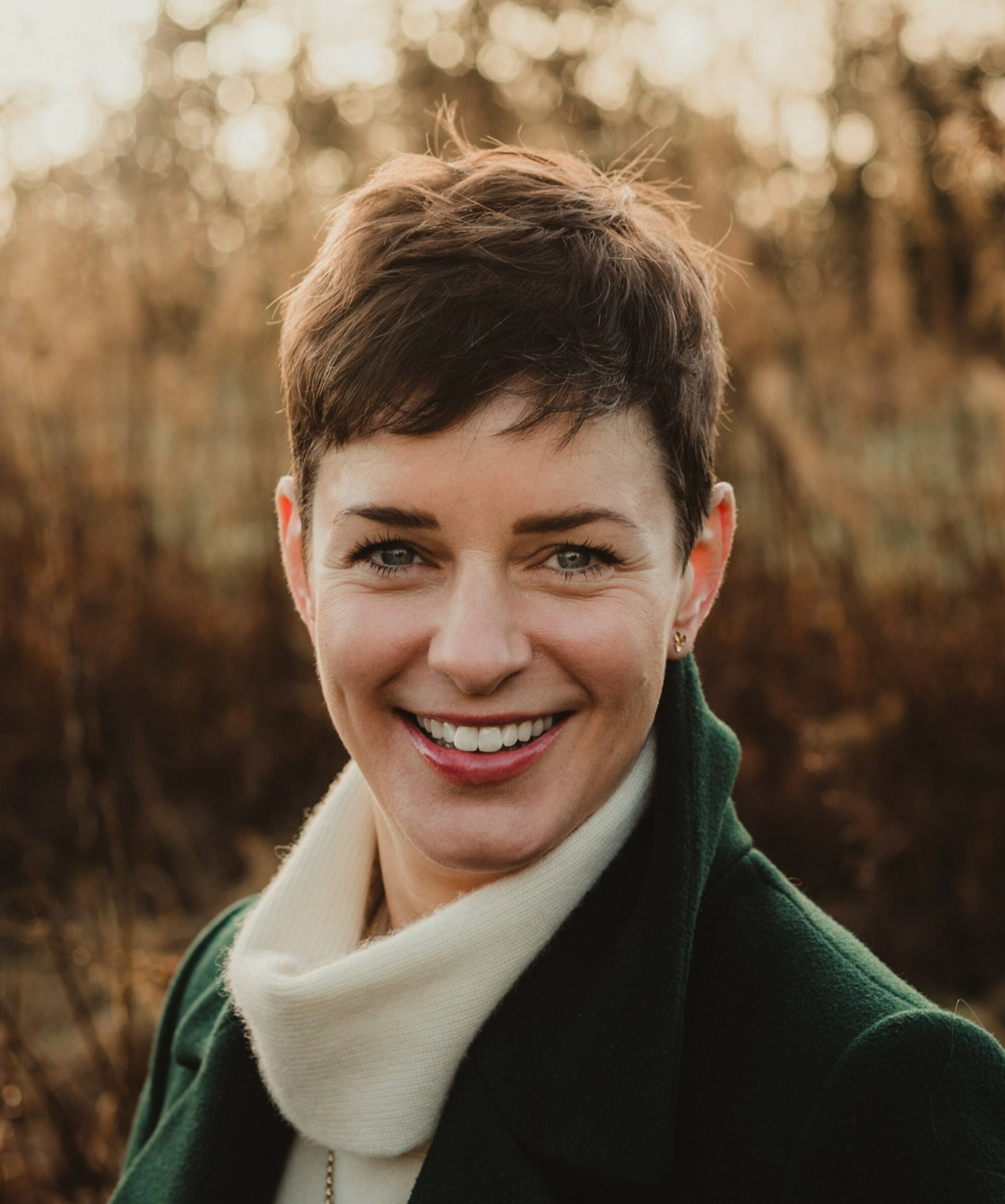
Prior to this, she spent four years as a strategy consultant and two in commercial & analytical roles in the FMCG and retail industries. She holds a degree in Natural Sciences & Management Studies from the University of Cambridge.
Andy and Sarah are supported by a highly experienced team of Non-Executive Directors and advisors, who bring both technical and commercial expertise to the business. This includes Chair Darran Messem, an experienced company director and NED with extensive ESG, governance, business development, sales and marketing expertise in transport, energy and the built environment.
minimass™ has signed a contract with property developer Ballymore for the design phase for two bridges - a cycle bridge and a footbridge - which will be built in late 2025 at Ballymore's Stonehaven residential development, currently onsite in Naas near Dublin, Ireland: https://lnkd.in/eS_s_sPb
This contract came off the back of the first-of-a-kind minimass™ pilot project, which was completed and launched in September 2024, having been awarded a prestigious Innovate UK Net Zero pre-commercialisation grant in July 2024 to fund this build. This was a fully instrumented 10.8m demonstrator footbridge at the Norfolk site of Constructionarium, a not-for-profit educational centre providing immersive experiential learning to students and professionals in the built environment sector. The centre offers 17 iconic civil & structural engineering projects, along with net zero and construction-related skills training.
The site provided an ideal location for the first minimass™ pilot due to the ability to trial new structures and techniques, the organisation’s fantastic reputation throughout the construction industry (particularly among engineers, contractors and academics), and the support of the onsite team during the build.
This project gives the industry a tangible example of success and proof of concept, including the procurement process, warranties and insurance, as well as the technical performance itself. Proving the minimass™ concept has demonstrated its suitability for superstructures in large building sectors as well as for the bridges sector.
Versus traditional steel or concrete footbridge designs (excluding foundations & prelims), the bridge provided an overall embodied carbon saving of 30% (keeping everything else but the beams the same i.e. decking, parapets etc), and a supply cost saving of 40%. The beams alone provided a carbon saving of 50%.
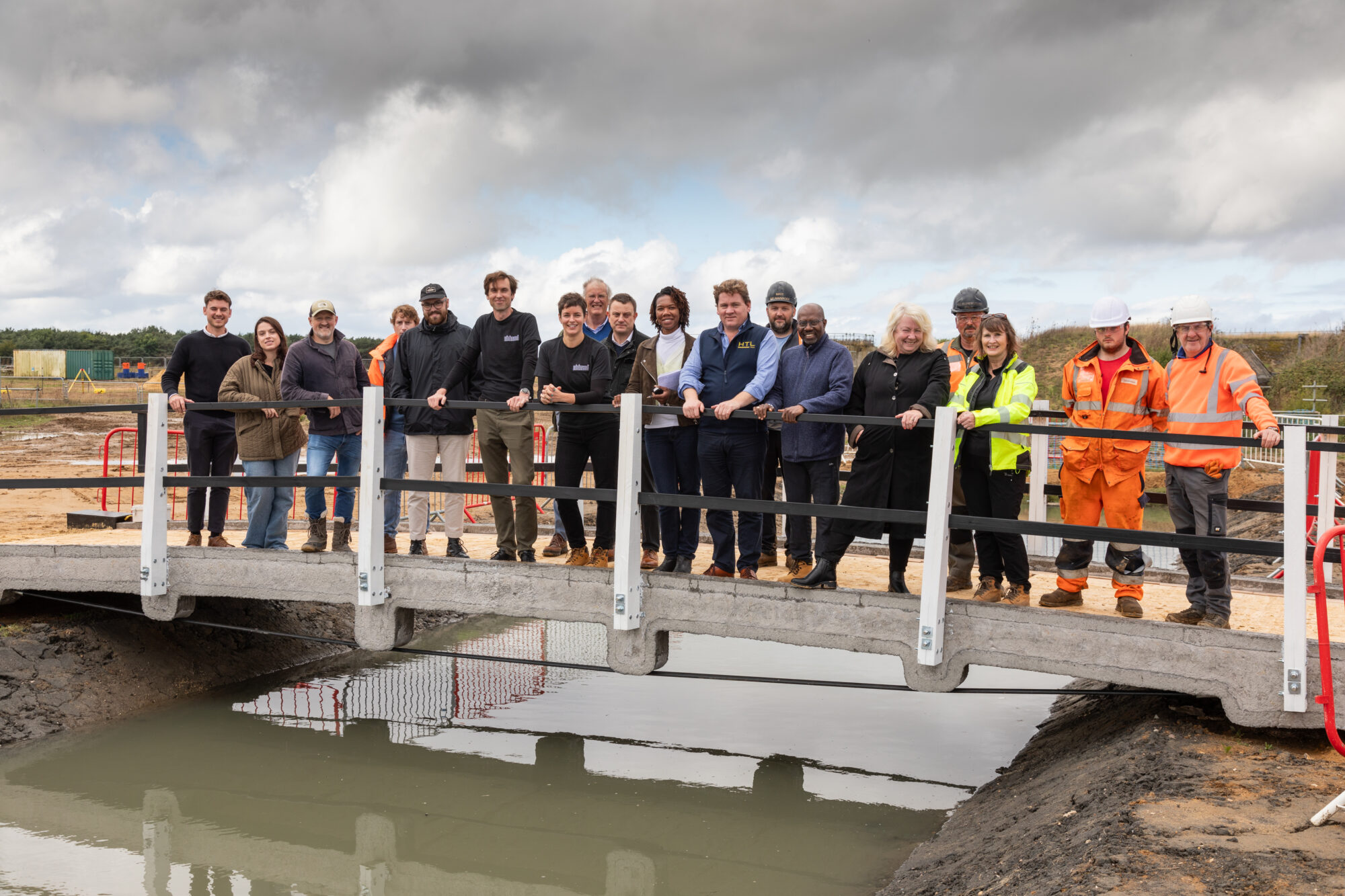
The footbridge includes:
• Two 10.8m minimass™ beams manufactured by our 3D printing partner HTL, with zero waste, which were produced & ready to transport in just 7 days;
• Timber decking - instead of concrete or steel - to further boost the low carbon credentials and showcase the ideal combination of minimass™ and timber to create a highly functional low carbon hybrid solution;
• State-of-the-art fibre optic sensors from infrastructure monitoring specialist Epsimon, which are allowing us to monitor the forces & temperature over a 6 month period. At this point the majority of material strength gain and creep effects will have occurred, enabling extrapolation of the long-term future performance of the full design life with a high degree of confidence.
Once 6 months of testing is complete, the bridge will be gifted to Constructionarium. One of the many benefits of minimass™ is the promotion of circularity - the bridge has been designed to be easily disassembled to allow it to join the centre’s project roster. This will help to educate the industry professionals of the future about sustainable and innovative construction solutions.
minimass™ is a concrete and steel truss which creates stiffness and strength through axial compression and tension, not typical bending and shear, using a similar approach seen elsewhere, such as the Pont du Truc de la Fare, in France.
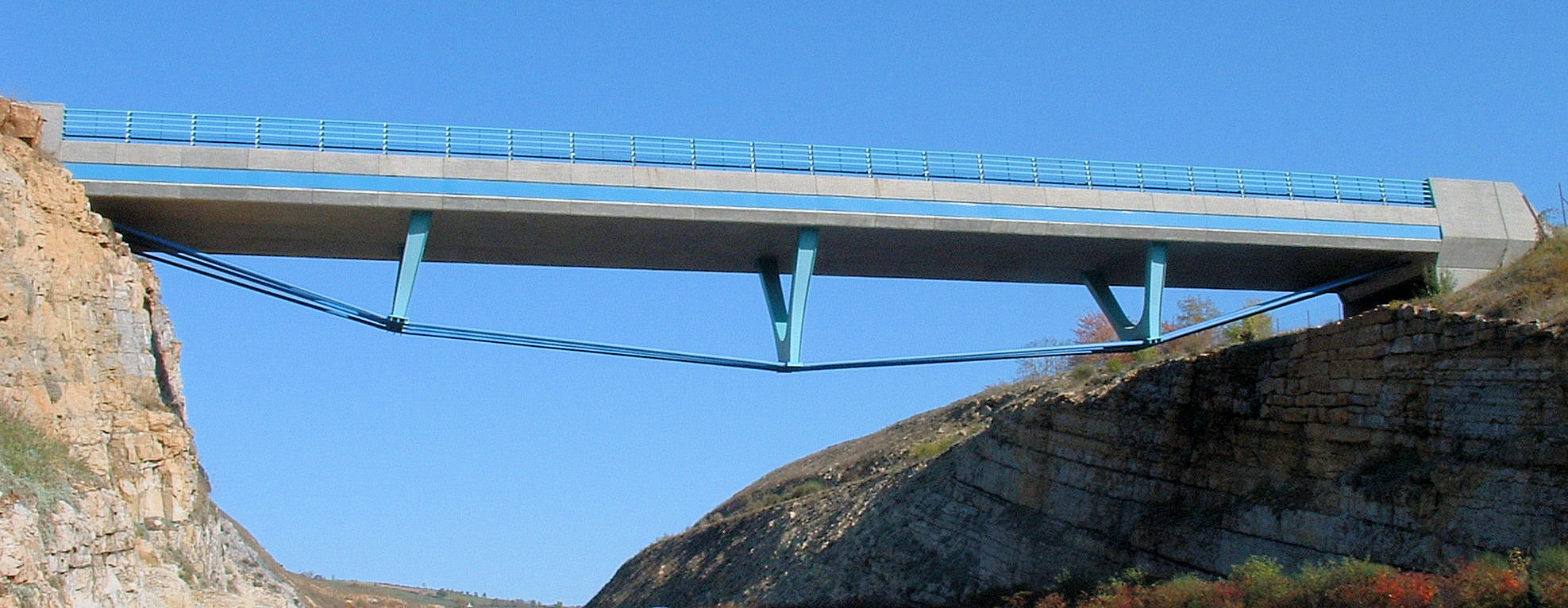
The patented geometry means that the top chord takes compression, the webs take compression and the bottom chord takes tension. The design approach uses graphic statics, inspired by the great engineers of the past. Standard design code methods, such as Eurocode 2 or ACI 318, are used to validate the strength and stiffness in the usual way.
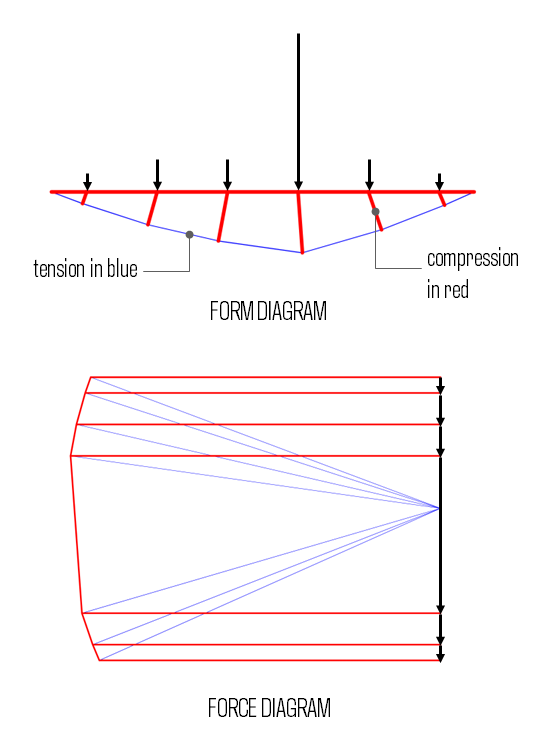
By forcing the concrete to remain in compression, it can be designed as unreinforced, vastly reducing the quantity of steel required.
These beams could be made using traditional methods e.g. pouring concrete into formwork. However, most structural elements are not standard components, and the new technique of 3d printing unlocks the potential of this design by allowing the fabrication of any number of bespoke beams at a fraction of the cost of traditional means - mass customisation.
· No formwork
· Minimal steel reinforcement
· Reduced labour costs
· Infinite scalability
The tension capacity is provided by standard post-tensioning steel cables, with standard post-tensioning anchors.
Simple details and standard components make this a robust design.
Updated load tables (date: 13/12/2024)
A series of 6m long physical prototypes have been printed and assembled for destructive load testing.
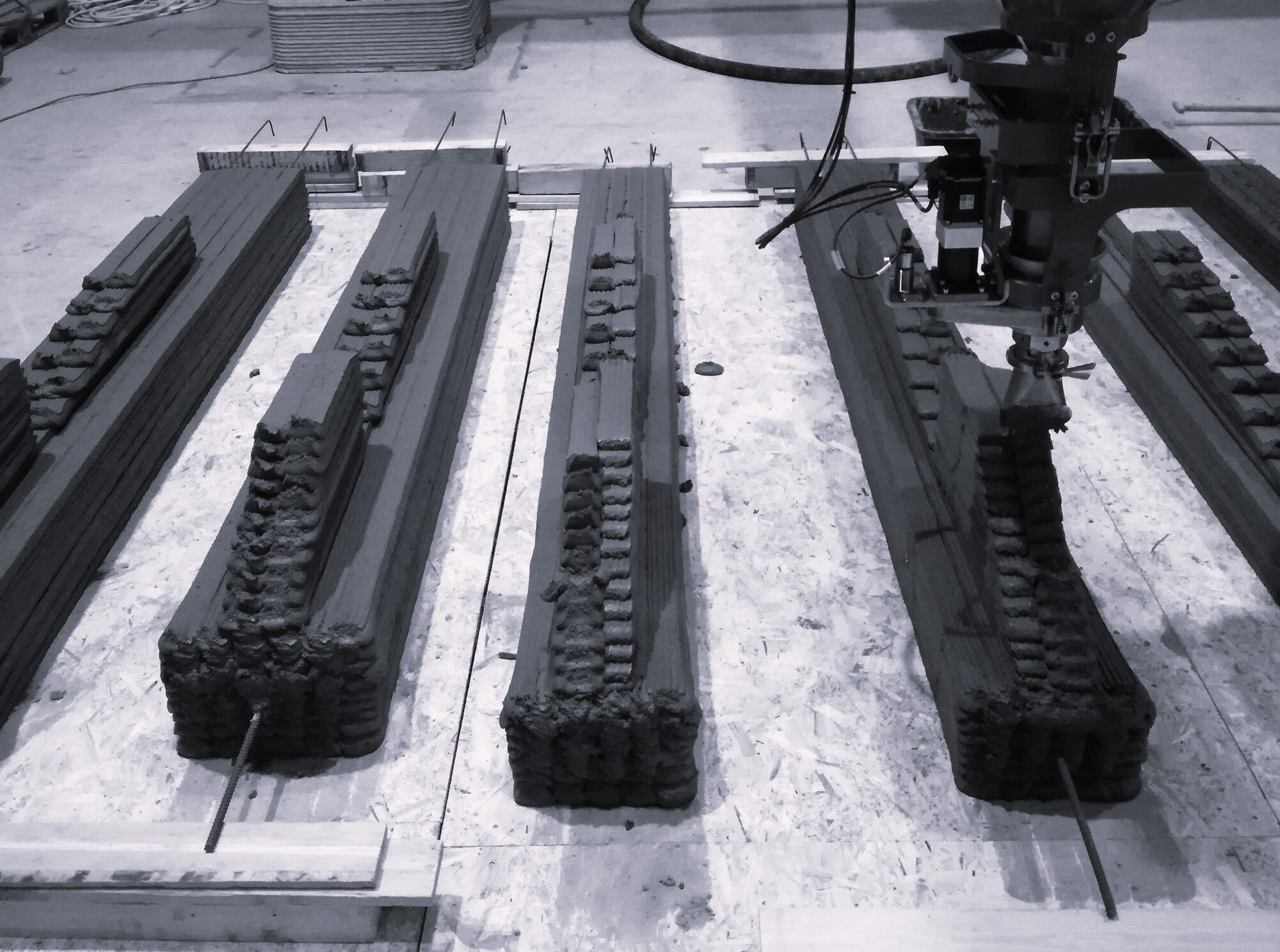
Working with a range of industry leaders, this testing process has been essential to validate minimass™ for the construction industry.
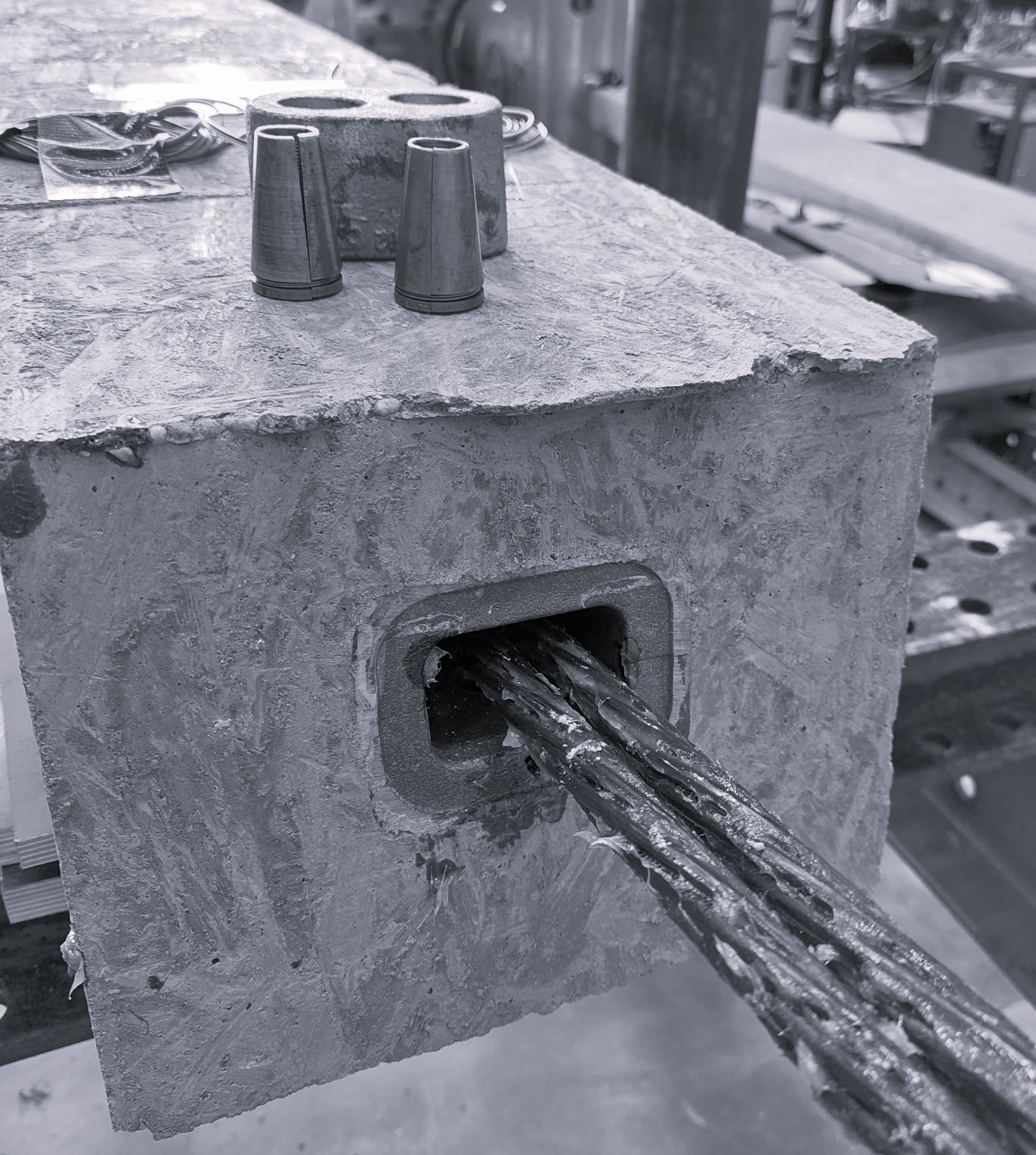
Destructive testing has been taking place using a 4-point bending test, with strain and displacement measurement throughout.
Contributors: COBOD International, CCL Scandinavia, PEIKKO, SIKA, Danish Technical University
For a full range of technical details, or to discuss how minimass™ might sit within a wider project context, please contact us.
However, there are some key considerations which all designers, clients and contractors must consider:
FIRE
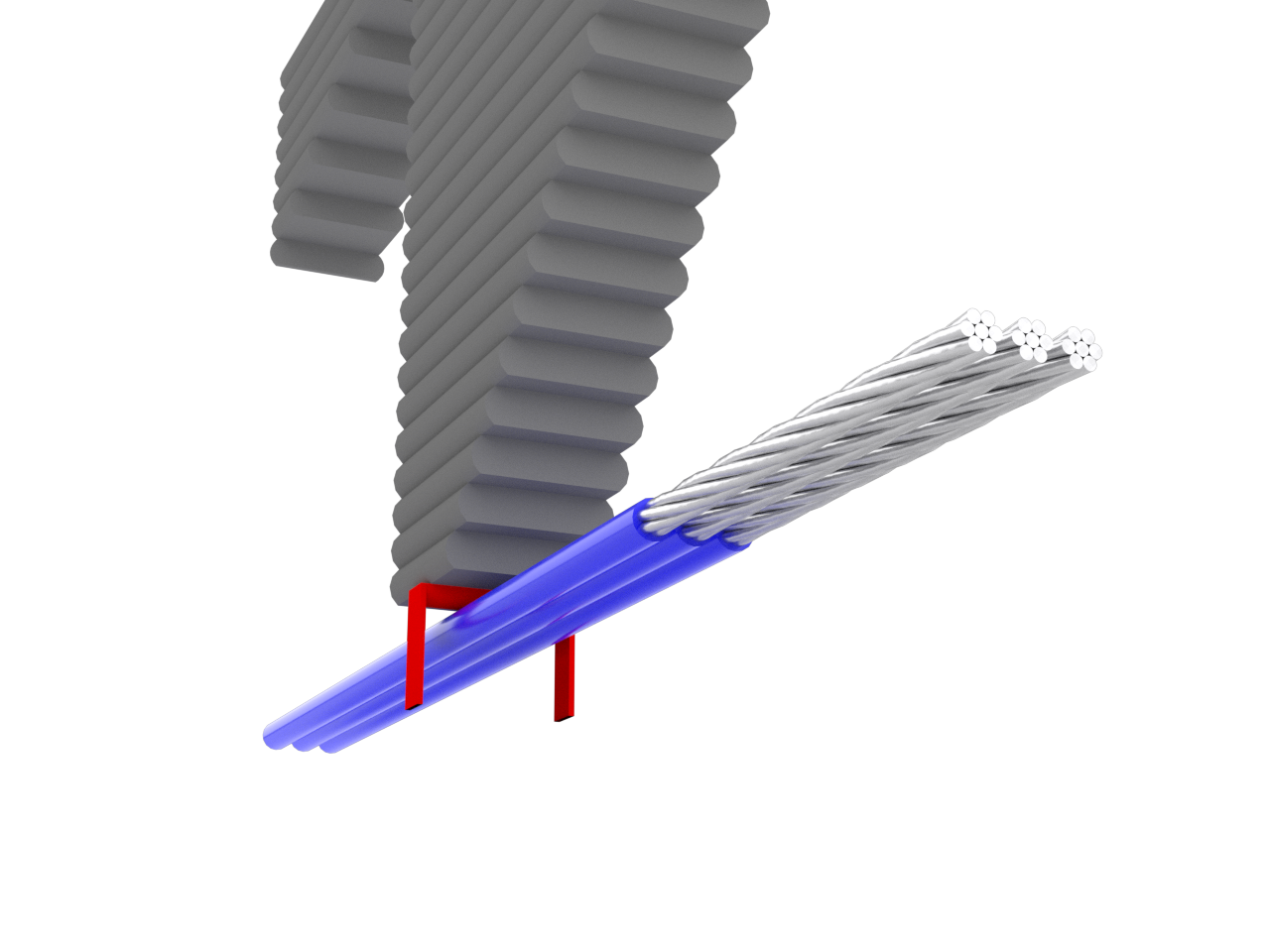
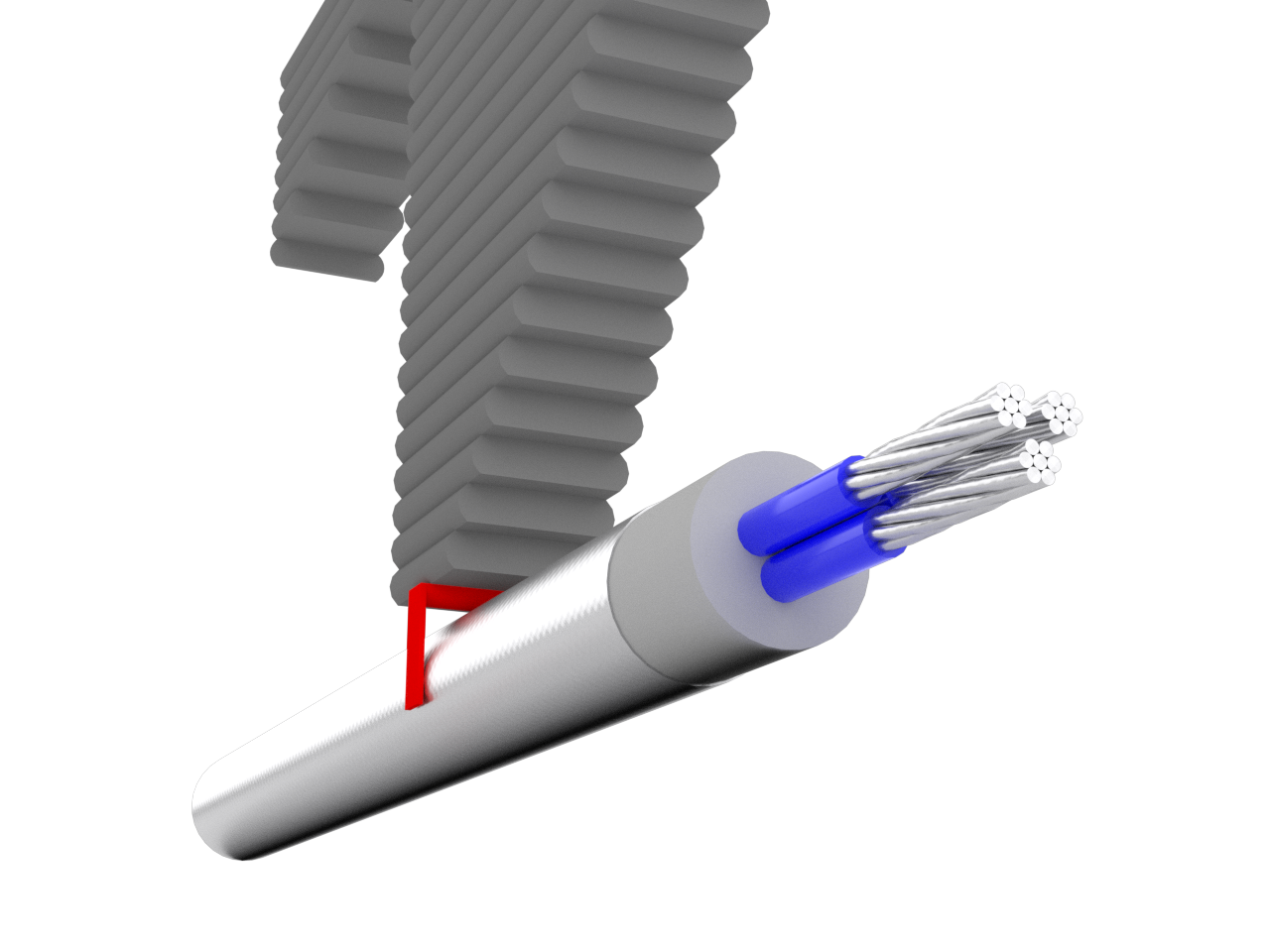
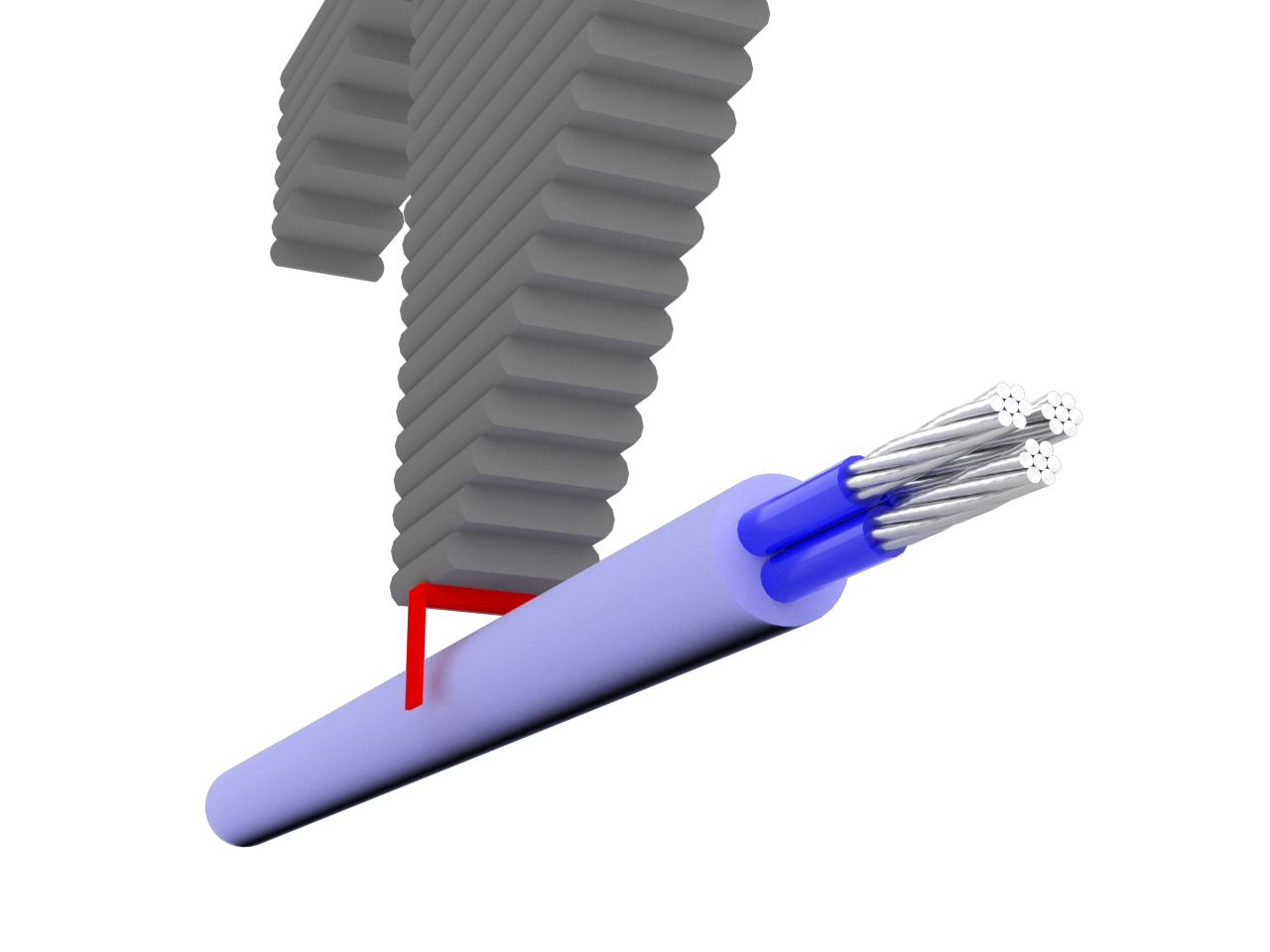
The concrete is fire resistant in the usual way. The steel cables are external to the concrete, so require a project-specific fire protection solution, with examples shown in the three images.
ROBUSTNESS
Beams in buildings are often required to resist forces associated with robustness or diaphragm effects. minimass™ provides the same effect by using the tension capacity of the steel cables. Horizontal tie force details at beam connections are available upon request.
TORSION
Being similar to a ‘T-beam’ in cross-section, minimass™ has a lower torsional capacity compared to a large rectangular beam. Therefore, the beam requires top flange restraint from connecting structure, such as a slab. During construction, it is necessary to provide temporary propping.
A torsion-resistant variation of minimass™ is currently under development.
minimass™ is a design, engineering and manufacturing solution. We are currently using traditional concrete and steel, but minimass™ is not limited in the choice of materials, nor by the manufacturing process - if sufficient identical elements are required, pre-casting is an option.
Concrete for 3d printing and beyond is a rapidly evolving field, with companies competing to produce stronger, cheaper materials with lower carbon emissions. minimass™ is leading the way, combining design, manufacture and materials to target net zero structural elements, and is future-proofed to work with low carbon materials.
Four UK patents and one US patent have been granted to date:
· UK patent granted: GB 2591831; ‘A structural truss, assembly and method of manufacture’.
· UK patent granted: GB 2591905; ‘A structural truss, assembly and method of manufacture’.
· UK patent granted: GB 2627779; 'A truss structure, assembly and method of manufacture'.
· UK patent granted: GB 2619012; 'A structural slab and method of manufacture'.
· US patent granted: US 12227945 B2; 'Structural truss, assembly and method of manufacture'.
Patent insurance is in place, for the protection of our intellectual property. Patents are being extended to the EU and US.
External recognition, media features & awards include:
· Winner of the Simmons + Simmons GreenTech Fund 2024, winning £25K of free legal advice. The Fund aims to encourage innovative solutions from around the world tackling the climate and biodiversity crises. See more about the fund here.
· 2nd place at the Innovation World Cup Smart Buildings Smart Construction in November 2023.
· Winner of the Build Offsite Innovation Challenge at UK Construction Week in October 2023.
· Shortlisted for the TechFest Innovation Accelerator Award in November 2024.
· Technical paper published in Structures, the research journal of The Institute of Structural Engineers in December 2023.
· Articles on the minimass™ pilot footbridge project published by:
- New Civil Engineer in October 2024 (see here)
- Concrete Magazine in their November 2024 edition (see here)
- Concrete Quarterly in their Autumn 2024 edition (see here).
· Letters of intent from five key industry players: Ballymore, Whitby Wood, Elliott Wood, BIG and Heyne Tillett Steel.
· The Australian Institute of Architects' Hearing Architecture podcast - Andy Coward: Fabrication Futures
· The Cambridge Tech podcast: Cambridge Cleantech special, featuring Sarah Blake
We have raised a total of £700K to date for minimass™ through venture capital, angel investors and public grant funding.
Key funding partners include Sustainable Ventures, a full-service ecosystem empowering sustainable start-ups to scale through community, investment, innovation, and workspace, and Innovate UK who have awarded us two grants.
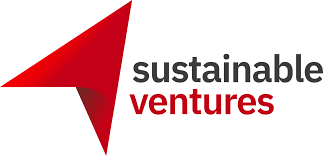
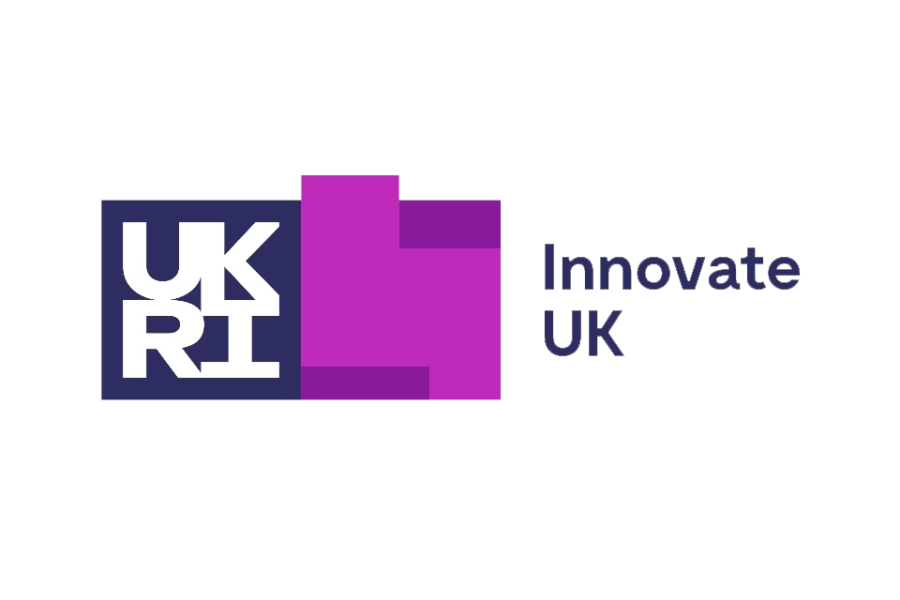
We are ready for pilot projects of all sizes, so we’d love to hear from you.
For more information, contact: info@minimass.net
LinkedIn: @minimass